DfMA’s Growing Popularity in Singapore
The construction industry has been slowly shifting towards working with DfMA. How does the DfMA change the construction industry, and how is the DfMA performing in the Singaporean construction scene?
by Sheldon Huang
|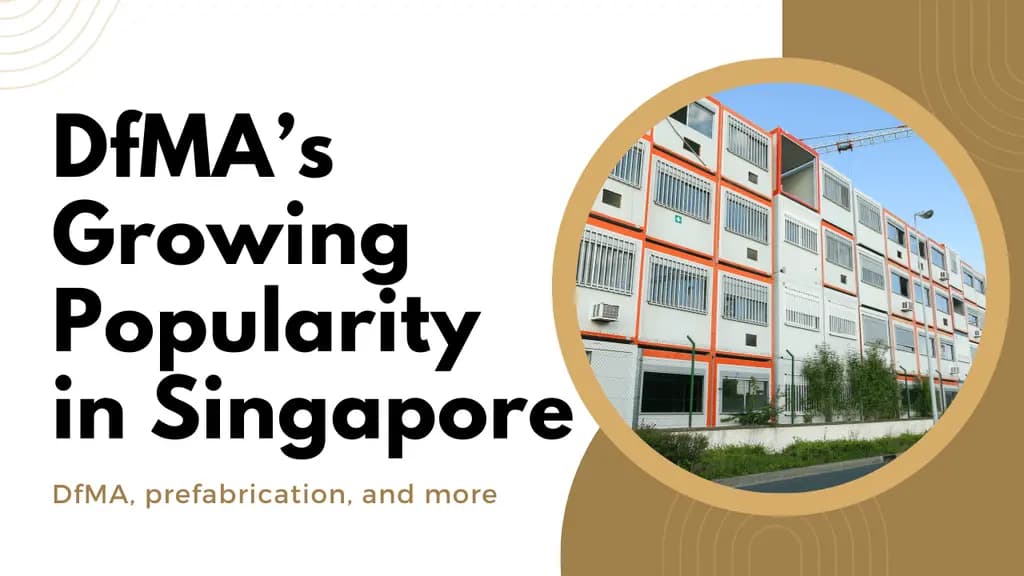
What is DfMA?
The Design for Manufacture and Assembly (DfMA) is way of manufacturing operation that optimizes a product’s supply chain to cut production costs and time. The DfMA focuses on the design of the product, more specifically, the design stage before production.
The engineering design of a product determines “70 to 80% of production costs.” Making changes to the initial design is the most effective in make products more cost effective. This is exactly why the DfMA is so effective in reducing costs.
The DfMA is actually the combination of what originally was Design for Manufacture (DfM) and Design for Assembly (DfA). Each provides different optimization for manufacturing procedures.
The Design for Manufacture (DfM)
The DfM changes how manufacturers make their products. Mostly, the DfMA saves contractors money through optimizing production processes and offering ease of manufacturing.
For example, one aspect the DfM advocates for is the use of standard parts rather than custom parts. Custom parts may require special tools, uncommon materials, or complicated production that may increase costs. For this reason, it is more ideal for manufacturers to employ standardized parts.
The Design for Assembly (DfA)
The DfA, on the other hand, focuses on the assembly of the product, whether by manufacturers or by customers. The DfA mostly reduces production costs by avoiding assembly mistakes and optimizing ease of assembly.
One of the most important designs of the DfA is reducing the number of parts for a single purpose. Not only does this reduce production costs, it also cuts storage costs, transportation costs, and potential mistakes in assembly.
How is Construction Changed by DfMA?
The DfMA rose in popularity around 30-40 years ago. Since then, various industries have adopted DfMA for manufacturing and production, including the construction industry. For construction projects, the application of DfMA elevates the entire manufacture and assembly process.
One pain point of construction teams is the condition of the work site.
The most uncontrollable factor is the weather. Rain makes the work site more dangerous to work at. The quality of the work and the entire construction inventory can also suffer from the weather.
Covering the workers’ necessities is both more difficult and more expensive when on-site. Transporting water and food to work sites is extremely money and time consuming. Cleanliness in work sites also become unstable, which can harm the workers’ health and wellbeing if severe.
For some work sites, the internet connectivity is questionable at best. If the team relies on digital management or communicates digitally, this can impede the team and significantly decrease productivity.
Transporting the necessary equipment and the workers also costs, not to mention equipment is prone to damages while transporting. The collective expenses if the project persists can cost contractors and firms a fortune.
The DfMA addresses the aforementioned challenges flawlessly. The DfMA encourages workers to build standardized modular designs. Then uses simple and safe designs, such as a snap fit, to combine the prefabricated modules. By working on raw materials beforehand in manufacturing plants, weather, necessities, connectivity, and transportation are no longer extra chores for contractors.
The DfMA not only fixes issues that cost contractors, but also provides multiple benefits that help the growth of a construction business.
Following the DfMA reduces in-site working hours. Workers work in manufacturing plants then only follow assembly steps on-site. This process is referred to as “prefabrication,” where teams manufacture the parts first then only work on-site when assembling.
This results in simpler on-site workflow, simpler construction logistics, and a lower overall cost. Moreover, it simplifies the production line and cuts time to market. Working DfMA-style is also more sustainable, as it reduces wastes, noise pollution, and carbon emissions from transportation.
Not only are visible and invisible unnecessary expenses saved, adopting the DfMA also helps businesses flourish by increasing the product quality and improve efficiency.
Incentivising the Adoption of DfMA
As mentioned above, shifting to working with the DfMA poses challenges to many contractors and tradespeople. Unfamiliarity, budget, and specialized equipment are each possible encounters to contractors.
Singapore, as one of the countries that extremely values the construction scene, provides incentives for firms to start and continue adopting the DfMA. The foremost help that the Singaporean government provided are the guidebooks regarding relevant techniques, insight, and considerations.
DfMA Resources
As the DfMA changes the construction industry drastically, there will be challenges and difficulties in how construction teams operate. Especially the part where teams have to prefabricate parts of the project before assembling on-site. This creates unfamiliarity among tradespeople.
For this reason, the Singaporean government introduced guidebooks for tradespeople working with different technologies. The guides are to help tradespeople better adapt to the DfMA way.
Advanced Precast Concrete System (APCS)
The APCS is dedicated to fabricating concrete parts. The Singaporean government also demands the project having 4 features under the “3S” principle of Standardization, Simplicity, and Single.
Mass Engineered Timber (MET)
MET is specialized in wood-related work. The guide from the Singaporean government provides certain wood-explicit risks for design inspection such as moisture levels, floor vibrations, and flammability.
Prefabricated Prefinished Volumetric Construction (PPVC)
This is for “free-standing 3-dimensional modules,” or in other words, pre-made rooms/houses. The document provides instructions on procedures a PPVC project contains, such as connecting joints, lifting the modules up, maintaining water-tightness, etc.
Prefabricated Bathroom Units (PBU)
As per its name, the PBU revolves around the construction of bathroom units. To a certain extent, PBU is similar to PPVC. Some requirements include bathroom accessibility, access to maintenance, repair, and replacement.
Prefabricated Mechanical Electrical and Plumbing (MEP) System
Exclusive to mechanical-related products, the MEP gives instructions regarding the prefabrication, quality control, and the installation of MEP modules.
Structural Steel
As steel already has “high strength to weight ratio,” the design guide for Structural Steel mostly contains techniques on welding and bolting prefabricated steel parts.
Funding Companies Adopting DfMA
Other than resource-wise support, the Singapore government also provides budget-wise support to substantially help construction firms wanting to adopt DfMA. The two initiatives being the Productivity Innovation Project (PIP), and the Productivity Solutions Grant (PSG).
Productivity Innovation Project (PIP)
The Productivity Innovation Project is one of the two incentives to encourage firms to adopt DfMA and continue the transformation towards better productivity.
Any “construction-related companies that are registered and located in Singapore are eligible to apply for support.” However, the applications are “evaluated based on the potential for productivity improvement on site. The trade productivity improvement should be at least 30%.” Once qualified, the PIP co-funds, on a reimbursement basis, projects for up to 70% of the qualifying costs.
Table for PIP Level of Support to Manufacturing Facilities Adopting DfMA
What’s worth noting is that the PIP co-funds different amounts to different qualified companies. In order to assess the type of productivity and the amount of funds, companies submit claims as a testimony after qualifying for the PIP. Claim documents include, but are not limited to:
- Progress and final reports
- Auditor statement of expenditure by an independent accountant
- Video of implemented system
- Claim statement
- Supporting claims documents (Such as: purchase orders, delivery orders, payment invoices, transaction records)
Productivity Solutions Grant (PSG)
Similar to the PIP, the Productivity Solution Grant co-funds companies for up to 50% of the qualifying costs. However, to be able to apply, there are certain requirements applicants must match.
- “The applicant must be a registered business in Singapore”
- “Have at least 30% local shareholding; and annual sales turnover of not more than $100mil or staff strength of not more than 200 employees”
- “Have its primary and/or secondary business activity in Construction and Facilities Management sub-sectors according to the Singapore Standard Industrial Classification Code (SSIC)”
- “The applicant’s purchase/subscription of the solution must be used in Singapore.”
Judging from the requirements, the one major difference between PIP and PSG is that PIP targets only Singaporean local Small and medium-sized enterprises (SMEs).
Conclusion
The DfMA transforms the construction industry fundamentally, as prefabricating construction parts was never the common way of construction.
Shifting to DfMA raises challenges to contractors. With resources and support the Singaporean government provides, it is optimistic that DfMA will become more widespread in Singapore.
For a sustainable approach to modular construction, consider integrating tools for better scheduling. Learn more in BIM On the Rise: What is Building Information Modeling.