Building Success: How Effective Inventory Management Transforms Your Construction Projects
Any construction team will find it difficult to complete a construction project without the use of any tools. For contractors, having the correct tools is one of the best ways to support the construction team and their construction business.
by Sheldon Huang
|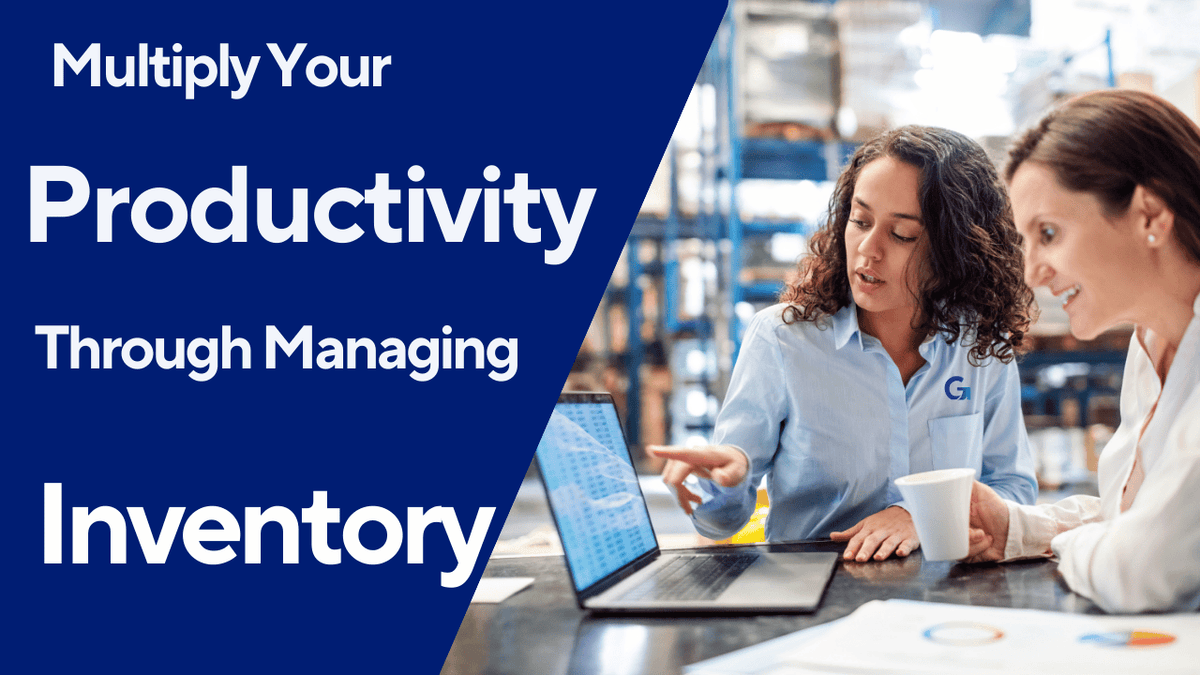
Countless contractors invest in physical assets like construction tools to aid their business. These investments are often necessary and can tremendously affect the progress of a project.
With that being said, many contractors do not realize how important it is to manage construction material and maintain tools. Even when making the right investments, they overlook this aspect of construction management.
As mentioned, tools make construction work extremely efficient. However, if there is not proper management and maintenance for these tools, how long will they be able to help?
Making business assets go a longer way than they originally should saves an immense amount of budget for businesses. This is why construction inventory management is essential for contractors anywhere.
Construction inventory management can be a complex concept, but some of the basic aspects of it include keeping asset information, updating information, and locating inventory.
Getting to Know Your Tools
“Understanding is the first step to managing.” The same applies to construction inventories. Some of the most important information to keep track of when managing tools includes the year of production, brand, model, status, expected maintenance/repair date, cost, expected lifespan, warranty, and much more.
The most straightforward way to do this is through paperwork, but this can be difficult considering the size of an inventory a contractor may have. If a construction team with a large inventory or a small construction team without excessive human resource manages its inventory through only paperwork, management becomes extremely tedious.
A more time-efficient way to do this would be through the cloud-based construction management software from Gobuid.
GoBuid offers a means of inventory tracking that takes less time and effort. Contractors can register all important asset information and create an organized catalog with just a few clicks. Imagine the time and stress saved when all this information is just a few clicks away.
Events that impede the progress of a project: a shortage of necessities like gloves or bottles; spending time to fetch equipment before realizing it’s under maintenance and only one is available for your construction site; not sending a piece of equipment to maintenance on time because the expected maintenance date wasn’t written; using a piece of worn-out/unmaintained equipment and causing potential injuries, none will get between a contractor and a successful construction project ever again with proper management and monitoring of a construction inventory.
Contractors and construction site managers should acknowledge the importance of construction inventory management in maximizing efficiency.
Maximize ROI with Preventative Maintenance
Preventative maintenance is another area where contractors can increase the longevity of their equipment and avoid unexpected expenses. Scheduling regular maintenance ensures that tools and machinery operate at peak efficiency, preventing breakdowns that could disrupt project timelines.
With GoBuid’s software, contractors can set automated reminders for when equipment maintenance is due. This ensures that no members would overlook tool and machinery conditions, reducing repair costs and extending the lifespan of valuable equipment.
Proper maintenance also plays a vital role in safety. Equipment failures can lead to accidents on the jobsite, which are not only dangerous but can result in costly legal liabilities. Keeping track of maintenance schedules and ensuring equipment status is critical for keeping your team safe and your projects running smoothly.
Sharing Info With Other Members
For teams that already have an established inventory management system, it may not be difficult to track an entire inventory. However, there is no purpose in keeping track of equipment if the contractors and the managers are the only ones having access to the information.
In a team, there are people who manage, and there are people who do the work. For this reason, it is essential that team members outside management roles also receive information regarding the inventory with promptness.
Similar to managing inventories, trying to achieve sharing information real-time when registering equipment information on physical copies of paperwork is extremely difficult.
Using a digital construction inventory management software, on the other hand, alleviates the difficulties of sharing information.
When making updates on equipment entries, all members of the same project receive the update immediately. This clears out any misunderstandings and mistakes regarding equipment’s availability.
Investing in construction management software benefits every member of the team. Adapting to use the right digital tools to assist management is a necessary change for contractors and construction professionals.
Can’t Find Something?
As mentioned above, tools and equipment are important investments to keep track of. For any tool to be stolen or lost would be a significant loss, especially for smaller construction firms and businesses. Even a missing box of nails would be a loss nonetheless. Contractors should keep these kinds of unnecessary losses from happening.
One way to prevent these unnecessary losses is through tracking equipment location. Traditionally, it is up to the equipment's user for the day to remember where it was, how long it was used, and when and where it was returned.
The flaws to this method are as obvious as it gets. If a piece of equipment does happen to get lost, there is no written record whatsoever. It is even more difficult to identify anyone to take accountability for the loss.
This is, of course, not a reliable way to manage equipment. Contractors then developed the paperwork method for workers and worksite managers to take responsibility for equipment by signing whenever taking out and returning equipment.
This method, despite being effective, is not efficient enough for the competitive construction industry.
A construction management software is capable of tracking more while using less time. The QR code scanning system by Gobuid allows contractors to produce a unique QR code for each equipment with just a few clicks, even on the mobile app. Put the QR codes on their corresponding equipment, and everything one has to do is just scan and leave, both when taking and returning equipment.
Proper tracking of a construction team’s inventory is critical, especially for small firms where there isn’t an excessive amount of resource for every jobsite.
Real-Time Insights for Smarter Decision Making
One of the biggest advantages of modern inventory management software is the ability to access real-time insights. These insights allow contractors to make smarter decisions about resource allocation, procurement, and project planning. By understanding trends in equipment usage and maintenance costs, contractors can optimize their operations and reduce waste.
For example, if data shows that a specific piece of machinery is frequently underutilized, a contractor might choose to rent it out for other projects, creating an additional revenue stream. Alternatively, if certain tools are breaking down more frequently than expected, contractors can proactively replace them before they cause major disruptions.
GoBuid’s software also integrates with other project management tools, providing a holistic view of your entire operation. This ensures that inventory management is not an isolated function but part of a broader strategy to enhance productivity and efficiency.
Benefits of Automating Inventory Management
While manual tracking methods may have worked in the past, the complexity of modern construction projects calls for more advanced tools. Automation is one of the key drivers in improving construction efficiency, and inventory management is no exception.
By automating inventory tasks, contractors can avoid many of the pitfalls associated with manual data entry and paper-based systems, such as errors, lost forms, or delayed updates. Additionally, automation helps contractors optimize resource allocation. Equipment and tools are valuable assets. not knowing where they are or when they’ll be available can severely harm productivity.
Through GoBuid’s project management software, contractors can streamline inventory processes, ensuring that equipment is available when and where it’s needed. By scanning the QR code during check-in and check-out, users can update the equipment status as 'To Repair,' 'Unavailable,' or 'Available,' helping managers stay informed about maintenance needs and equipment availability. This process reduces project downtime and helps prevent costly oversights by ensuring that key resources are properly tracked and maintained.
Conclusion
Optimizing construction inventory management doesn’t just happen at the jobsite—it starts with using the right tools for managing those assets. By leveraging GoBuid’s construction management software, contractors can streamline their processes, reduce costs, and maximize productivity.
Investing in smarter ways to manage inventory not only ensures efficiency but also helps contractors stay ahead in the construction industry. Whether it’s through automated tracking, preventative maintenance, or real-time insights, modern tools like GoBuid offer the solutions contractors need to succeed.
Construction is already challenging enough; managing your equipment and tools shouldn’t add to the complexity. By optimizing inventory management, contractors can focus on what matters—delivering high-quality projects on time and on budget.